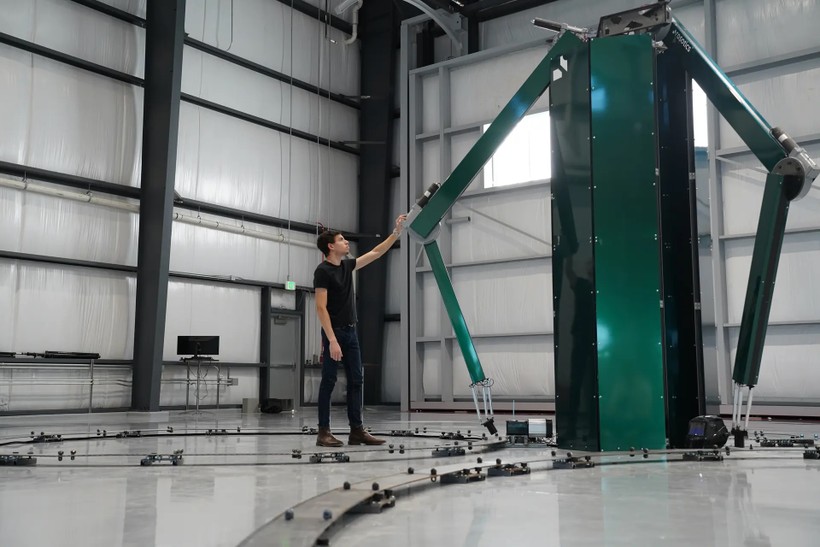
Công ty Rosotics tại Arizona tuyên bố sẵn sàng cách mạng hóa kỹ thuật in kim loại 3D quy mô lớn, sử dụng phương pháp "in cảm ứng nhanh" mới, có thể in những bộ phận có kích thước khổng lồ với những ưu thế cơ bản như tốc độ, chi phí, an toàn và hiệu quả sử dụng năng lượng cao.
Sản xuất các bộ phận kim loại bằng công nghệ in 3D bồi đắp có thể được thực hiện theo một số phương pháp, nhưng ý tưởng chung tương tự: nhà sản xuất chạy một máy in lớn để lắng đọng kim loại nóng chảy thành từng lớp trên một chất nền, sau đó hợp nhất lại thành một cấu trúc thể rắn. Bằng phương pháp in 3D từ nguyên vật liệu, nhà sản xuất có thể tạo ra những hình dạng mà phương pháp sản xuất cắt gọt kim loại truyền thống không thể thực hiện được. Mặc dù quá chậm và khó ứng dụng để sản xuất hàng loạt, nhưng đây là một kỹ thuật cực kỳ nhanh và hiệu quả đối với những bộ phận chi tiết nhỏ và tạo nguyên mẫu nhanh.
Nhiều hệ thống in kim loại hiện nay sử dụng tia laser để gia nhiệt và làm tan chảy nguyên liệu kim loại dạng bột hoặc dây. Người sáng lập và là Giám đốc điều hành của Rosotics Christian LaRosa cho biết, có một số thách thức cố hữu trong những hệ thống in 3D laser:
Thứ nhất, nguyên liệu kim loại dạng bột rất đắt tiền và nguy hiểm như titan dạng bột dễ nổ.
Thứ hai, laser là một phương tiện kém hiệu quả để chuyển năng lượng thành nhiệt. Những hệ thống in 3D trên nền tảng công nghệ laser quy mô lớn đòi hỏi phải có các hệ thống cung cấp năng lượng đặc biệt.
Thứ ba, chùm tia laser công suất lớn rất nguy hiểm, sự phản xạ của một chùm năng lượng đủ để làm mù một người nếu bị chiếu thẳng vào mắt.
Thứ tư, những bộ phận được chế tạo ra bằng các phương pháp trên cơ sở in laser thường cần được xử lý nhiệt, có nghĩa là chỉ có thể in những bộ phận lớn bằng lò nướng mà nhà sản xuất có thể nướng chi tiết sau đó.
Giám đốc điều hành công ty Rosostics Christian LaRosa cho biết, ông phát minh ra một phương pháp in 3D thay thế, giải quyết tất cả những thách thức này, mở ra khả năng in những bộ phận kim loại khổng lồ với giá rẻ, dễ dàng và nhanh chóng, đủ lớn để sử dụng trong những cấu trúc của máy bay, tên lửa và các phương tiện giao thông lớn. Rosotics thiết kế, chế tạo và thử nghiệm thành công một loại đầu in 3D kim loại mới, được gọi là Mantis, truyền nhiệt tới nguyên liệu kim loại với hiệu quả cao trên cơ sở cảm ứng.
LaRosa trong cuộc phỏng vấn với New Atlas trực tuyến cho biết: "Theo tôi, đó là một phương pháp rất tự nhiên để in 3D kim loại. Nhà sản xuất tạo ra một trường điện từ từ một cuộn dây, bất kỳ kim loại sắt từ nào đi qua trường đó đều bị nung nóng theo phương thức tự cảm do dòng điện xoáy đang tạo ra trong kim loại. Chúng tôi loại bỏ tia laser khỏi quy trình và đơn giản là đưa dây điện qua một vòi phun, gia nhiệt theo phương thức cảm ứng khi kim loại đi qua. Chúng tôi gọi kỹ thuật này là In cảm ứng nhanh (RIP). Kỹ thuật sáng tạo này giúp nhà sản xuất đạt được mục tiêu tương tự với tổn thất năng lượng ít hơn nhiều."
Quy trình hiệu quả hơn bao nhiêu?
Ông LaRosa nói: “Hiệu quả trong một quy trình trên cơ sở công nghệ laser, theo nhiều phương thức khác nhau đều rất thấp. Đó là một phương thức sử dụng quang học để truyền nhiệt. Chuyển sang quy trình cảm ứng, nhà sản xuất tăng cường hiệu quả rất nhiều. So với phương pháp lắng đọng năng lượng trực tiếp, phương pháp in 3D tiếp liệu dây trên cơ sở sử dụng laser, kỹ thuật của chúng tôi có hiệu suất cao hơn 30-50% hiệu quả trên tổng năng lượng sử dụng. So với những phương thức sử dụng năng lượng khác, kỹ thuật này hơn hẳn một cấp độ."
![]() |
Christian LaRosa (giữa) với các thành viên của đội Rosotics vừa giành được kỷ lục in 3D kim loại. Ảnh Rosotics |
LaRosa cho biết: “Nguyên liệu cũng không nhất thiết phải là sắt từ. Nhôm là một mục tiêu lớn đang được hướng tới do vật liệu tổng hợp tạo thành cơ sở cho rất nhiều bộ phận cấu trúc trong hàng không vũ trụ không có từ tính một chút nào. Chính vì vậy, chúng tôi tìm ra những phương pháp độc đáo làm nóng nguyên liệu theo phương thức tự cảm, sử dụng những phương pháp tiếp cận đột phá trong khoa học luyện kim. Nhà sản xuất có thể làm nóng vật liệu theo phương thức tự cảm hoặc có thể cho nguyên liệu mục tiêu di chuyển qua một kênh dẫn, làm nóng theo phương thức tự cảm để truyền nhiệt nhờ tiếp xúc vật lý."
Thiết bị in 3D bằng cảm ứng chạy ngoài trời, sử dụng ổ cắm 240V công nghiệp thông thường. Mantis có thể in những bộ phận cấu trúc cho những khách hàng hàng không vũ trụ mà trước đây gần như không thể. Kỹ thuật này mở ra một quy trình chế tạo mọi bộ phận với các loại kim loại.
![]() |
Thiết bị hoạt động môi trường mở, sử dụng ổ cắm 240V công nghiệp thông thường, Mantis có thể in các bộ phận cấu trúc cho hàng không vũ trụ. Ảnh Rosotics |
Công ty đã thử nghiệm rộng rãi với nguyên liệu là thép và nhôm. Ông LaRosa cho biết Mantis có thể xử lý hầu hết mọi kim loại: "Từ những gì chúng tôi thực hiện, những vật liệu, được sử dụng rộng rãi trong hàng không vũ trụ, kỹ thuật mới đều có thể xử lý hiệu quả. Có khả năng nhiều vật liệu sẽ vượt quá giới hạn, nhưng ngay cả khi đó, Robostics vẫn có thể thay đổi quy trình và giải quyết cả những vấn đề đó. Titanium là một vật liệu khá khả thi, một số vật liệu khác chúng tôi đang kiểm tra. Một trong những vật liệu có thể thực hiện được ngay là đồng niken, có hiệu suất cơ học rất tốt trong một số mục đích sử dụng. Nhìn chung, quy trình này hoạt động hiệu quả với bất kỳ vật liệu nào có sẵn trên thị trường ở dạng dây."
Máy in hiện xử lý những dây kim loại có đường kính từ 1-10 mm, ông LaRosa cho biết, có thể dễ dàng mở rộng quy mô khi cần, chỉ bằng cách đơn giản là mở rộng các đầu phun.
Rosotics đã xây dựng một nguyên mẫu. Ông LaRosa nói: "Có một nguyên mẫu máy in kích thước đầy đủ, in được các bộ phận có chiều rộng khoảng 26 feet (8 m) và chiều cao khoảng 20 feet (6,1 m). Chiếc máy này đang chạy 3 đầu phun, mỗi đầu đẩy hơn 15 kg (33 lb) kim loại một chút trong 1 giờ. Là một hệ thống, nguyên mẫu có thể in khoảng 50 kg kim loại (110 lb)/1 giờ. Hệ thống chạy bằng ổ cắm điện 240V từ bất kỳ ổ cắm thông thường nào trong môi trường nhà kho, một lợi thế mà nếu nhà sản xuất đang vận hành một máy in laser sử dụng dây kim loại quy mô lớn, buộc phải tìm cách liên hệ với công ty điện lực để có được đường dây điện cao thế. Sử dụng kỹ thuật này, toàn bộ quy trình được đơn giản hóa.
"Quy trình của chúng tôi cũng hoạt động trong không gian mở, vì vậy nhà sản xuất không cần phải in các bộ phận trong buồng chân không. Với các quy trình trên cơ sở công nghệ laser, cần phải đốt nóng toàn bộ cấu trúc đồng đều nhằm giảm ứng suất dư trong quá trình in gây ra. Kỹ thuật này không phải thực hiện loại thao tác đó sau khi in do bộ phận đã được gia nhiệt cảm ứng. Lợi thế này đơn giản hóa toàn bộ quy trình in 3D."
![]() |
Hệ thống Mantis có thể in các cụm hình trụ khổng lồ bằng kim loại. Ảnh Rosotics |
Quy trình RIP khiến toàn bộ quá trình nhanh và rẻ hơn nhiều, đồng thời mở ra quy mô in 3D kim loại với kích thước gần như vô hạn. Ông LaRosa nhận xét, in 3D đã cách mạng hóa quá trình sản xuất và phương thức chế tạo các bộ phận nhưng bị giới hạn bởi kích thước. Kỹ thuật mới đã khắc phục những hạn chế này trong công nghệ in kim loại.
Hệ thống in 3D cảm ứng rất phù hợp cho những ứng dụng kết cấu phức tạp như cấu trúc của tên lửa hoặc xe tăng. Bất kỳ loại bộ phận cấu trúc nào mà ngành hàng không vũ trụ yêu cầu, hệ thống in 3D của Robostics đều có thể chế tạo được.
Hệ thống được thiết kế để ứng dụng cho ngành công nghiệp nặng như ngành năng lượng, xây dựng, hàng hải, giao thông, kỹ thuật mới có thể phục vụ rất tốt cho những ngành này.
Christian LaRosa nhấn mạnh: “Đối với bất cứ thứ gì lớn hơn tủ lạnh, phương thức tiếp cận này sẽ sẽ giải quyết triệt để và nhanh chóng. In 3D kích thước lớn đơn giản là không thành vấn đề.”
Được thành lập vào năm 2019, Rosotics hoàn thành vòng tài trợ trị giá 750.000 USD vào tháng 11/2022.
Theo New Atlas
Bình luận của bạn đọc
Bình luận bằng tài khoản VietTimes
Bình luận bằng tài khoản mạng xã hội
Xin vui lòng gõ tiếng Việt có dấu